Checking Out the Globe of Steel Stamping: From Layout to Manufacturing
Within the realm of production, steel marking stands out as an accurate and effective technique for forming steel sheets right into numerous forms with amazing consistency. From the preliminary style phase where elaborate patterns materialize to the complex manufacturing procedures, steel marking is a mix of virtuosity and design. Diving right into this globe reveals a complicated interplay of creative thinking and technical mastery, providing a peek into a realm where innovation meets workmanship.
Background of Metal Stamping
Steel marking, an extensively utilized manufacturing process today, has an abundant background that goes back to ancient times (Metal Stamping). The origins of steel stamping can be mapped to ancient worlds such as the Egyptians, who used marking methods to decorate jewelry and ornaments with intricate styles. In time, metal marking evolved, with human beings like the Greeks and Romans utilizing it for developing coins and attractive items

In the 20th century, metal marking remained to advance with the combination of automation and computer system numerical control (CNC) modern technology. These improvements further boosted the performance and accuracy of steel stamping procedures, making it an important part of contemporary production across sectors such as automobile, aerospace, and electronic devices. Today, metal marking continues to be an important production process, integrating practice with development to satisfy the demands of a constantly progressing sector.
Design Considerations and Prototyping
When creating metal stamping jobs, meticulous attention to make considerations and prototyping is necessary for ensuring ideal production end results. Design considerations in metal marking consist of product selection, part geometry, tooling style, and manufacturing usefulness. Choosing the best material is vital as it influences the component's performance, cost, and manufacturability. Part geometry influences the complexity of the stamping procedure and the performance of the end product. Tooling layout plays a substantial role in the success of metal stamping projects, impacting part accuracy, tool durability, and production effectiveness.
Prototyping is a critical phase in the steel marking procedure that enables engineers to test the design, confirm manufacturability, and make essential changes before full-blown production. Prototyping aids recognize prospective problems at an early stage, saving time and prices over time. It likewise supplies a chance to maximize visit this page the style for effectiveness and quality. By carefully taking into consideration style aspects and utilizing prototyping, suppliers can streamline the metal stamping process and attain premium, affordable manufacturing end results.
Tooling and Devices Basics
Taking into consideration the important duty that tooling layout plays in the success of steel marking click to investigate jobs, comprehending the necessary devices and devices needed is critical for achieving efficient manufacturing end results. Components hold the metal in area throughout the stamping procedure, ensuring precision and repeatability. Spending in high-quality tooling and equipment not just boosts production efficiency but additionally leads to greater accuracy, lowered waste, and total expense savings in steel marking operations.
Manufacturing Refine and Quality Assurance
Efficiently managing the manufacturing process and executing durable quality assurance steps are essential for making certain the success of steel stamping tasks. The production procedure in metal marking includes a series of actions that should be meticulously collaborated to achieve ideal results. It starts with the preparation of raw products, followed by the arrangement of the stamping tools and tooling. Operators then feed the products into the press, where the marking operation More Help occurs. Throughout this process, it is critical to keep track of the assembly line for any type of concerns that may impact the quality of the stamped parts.
Quality control in metal stamping is paramount to supply items that meet the required requirements. By preserving stringent quality control criteria, makers can maintain their credibility for delivering high-grade steel stamped items.
Applications and Market Insights
In the realm of metal marking, the successful application of manufacturing processes and quality control actions straight influences the performance and dependability of various market applications and offers beneficial understandings into the market's operational characteristics. Metal marking finds prevalent application across varied industries, consisting of automobile, aerospace, electronic devices, and home appliances. In the automotive market, steel stamping plays an essential duty in producing elements such as chassis, braces, and architectural parts with high accuracy and efficiency. The aerospace market counts on metal marking for manufacturing complex components like panels, braces, and fittings that satisfy strict high quality requirements (Metal Stamping). In the electronic devices industry, metal marking is used to produce specific components like ports, terminals, and warmth sinks. Additionally, metal marking helps with the production of numerous home devices, consisting of refrigerators, washing makers, and stoves, by providing economical remedies for making durable and complicated components. Understanding the applications and market understandings of steel marking is essential for optimizing production processes and improving item top quality throughout different industries.
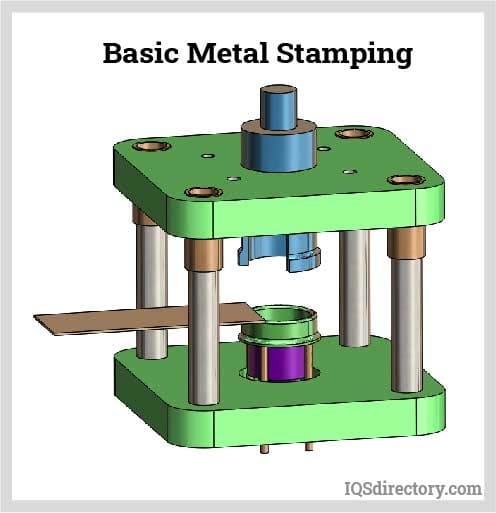
Verdict
Design factors to consider, prototyping, tooling, equipment, manufacturing processes, and top quality control are important facets of steel marking. With its widespread applications and sector insights, steel marking continues to be a functional and efficient production process.